Stainless steel polishing machine
Supplier Specialist in stainless steel equipment for tanks and machines, DVAI proposes the automatic polishing of tank heads, cones and shells thanks to a fleet of CNC machines. Revolution polishing provides a uniform appearance and controlled roughness.
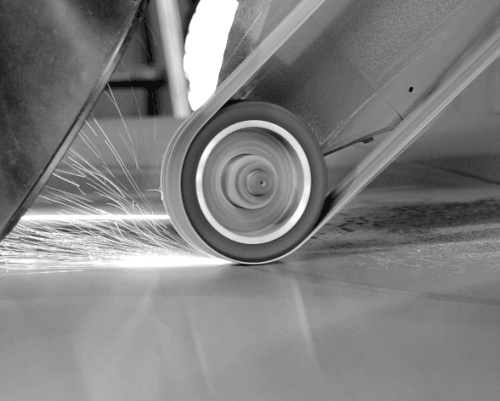
The advantages of stainless polishing at DVAI
With grain imposition (From GR40 grain 40 for the highest thickness to grain 400 gr400) or a roughness value (from Ra 3.2 μm to Ra 0.4 μm mini) DVAI delivers your tank heads and polished shells. The polishing is protected by a PVC film applied after control.
Dans le cas de polissage de viroles, DVAI fabrique à partir de tôles brutes et réalise le polissage intégral après formage. La soudure est donc polie simultanément à la virole, ce qui permet d’obtenir un aspect beaucoup plus uniforme que le résultat obtenu par formage de tôles pré-polies puis de reprise manuelle la zone de soudure. L’aspect final extérieur est donc beaucoup plus qualitatif et esthétique. L’acier inoxydable est un métal parfaitement adapté au polissage.
In the case of polishing shells, DVAI manufactures from blank sheets and makes the complete polishing after forming. The weld is therefore polished simultaneously with the shell, which makes it possible to obtain a much more uniform appearance than the result obtained by forming pre-polished sheets and then manually resetting the welding zone. The external appearance is therefore much more qualitative and aesthetic. Stainless steel is a metal perfectly suited for polishing.
Automatic polishing saves time
DVAI polishes your pieces within the same production site, which reduces the manufacturing time and considerably reduces logistics costs. This also reduces the risk of marks related to possible shocks during transport.
DVAI holds cold-rolled sheet up to 6mm in stock to enable machine polishing to be carried out even on thin layers.
DVAI is equipped with rotating machines, that is to say that the polishing can be performed on any part of revolution. The workpiece is positioned on the turntable and brought into contact with a polishing head which follows the profile of the workpiece during rotation.
The circular movements of the polisher allow a regular friction and thus a homogeneous polishing that shines the sheet. The polishing head polishes the workpiece on a contact area which represents a thin polished band. This thin strip advances along the profile of the piece and is covered as it rotates to polish the surface of the complete piece. The appearance is very homogeneous and we can guess the trace of the snail-shaped polishing head with differences in light that polish the polish.
Type of pieces to polish
Automatic polishing on a turntable is possible for a large number of revolution pieces :
- discs: possible for heavy thicknesses. Polishing 1 or 2 faces to see according to thickness and diameter
- dished heads: internal polishing / external polishing / possibility of polishing only a bottom area (only edge radius, area between 2 diameters).
- flat heads : depending on the thickness, diameter and polishing to be done. Do not hesitate to consult our sales department to study the feasibility of polishing your room.
- conical heads : internal polishing / external polishing / 2 polished faces
- shells : external polishing in only one “pass” for shells of height lower than 3m / feasibility of the internal polishing according to the diameter and the height of the shell.
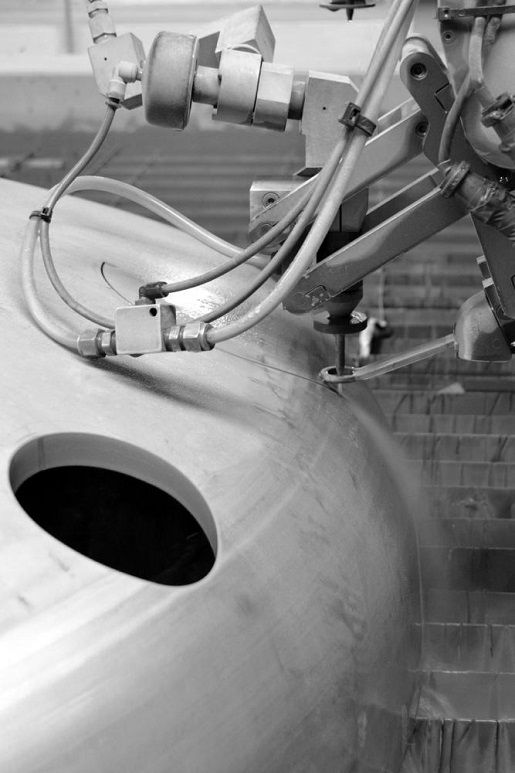
Cut out openings on a polished background
In addition to polishing, DVAI produces on your dished heads, flat or conical, the drilling and the openings with water cut technology. This cutting process is very suitable for drilling and cutting of polished pieces safely. Indeed, the cut can be made without impact on its quality even through PVC protection films (1 side or 2 sides), which makes it the ideal cutting means for the realization of openings for the stitching polished bottom.
To know about the polishing of stainless steel
When you have stainless steel pieces to polish, you are often faced with 2 possible problems :
Steel polishing for aesthetic appearance
Make a polishing for a visual rendering of the piece: the objective is mainly to obtain an aesthetic appearance for this piece and to obtain a satin or shiny aspect. We speak then most often in grain (polishing GR180 for example). The abrasive strips are successively passed from the largest grain possible to the finest grain until the requested finish. A final pass is made at the end of the process to perfect the appearance. The gloss at the end of polishing is then ensured by the passage of an abrasive finishing tape. However, DVAI can not offer polishing with a mirror-polished effect on stainless steel.
The strongest grain starting depends on the thickness of the sheets. For sheets from 6mm, it is often necessary to start with a 40 grit (GR40). These abrasive strips of coarse grain are similar to an emery cloth specially adapted for polishing. This first phase of preparation can be accompanied by manual grinding to eliminate defects especially for thick pieces : the polisher must manually grind the unevenness of the sheet in order to better prepare the workpiece before automatic polishing. This operation is done with a flap disc or a grinder with suitable abrasive discs and a flat grinding. No abrasive belt passes should be neglected to ensure regular and uniform polishing and the grains must be mounted during polishing by the polisher in a regular and rigorous manner.
How to polish to obtain roughness
Get maximum roughness on the sheet is related to the constraints of your process or your field of activity. The roughness measured in Ra using a specific device (a roughness meter) is then carried out according to your specifications by passing the successive bands until obtaining the requested Ra (checked by roughness sampling). For simplicity, if we look at a sheet at the microscopic scale, we can see that the structure of the raw sheet is not perfectly smooth but composed of small infractuosities. The roughness corresponds to the maximum distance measured in height at these infractuosities and is measured in μm. Polishing smooths the sheet and reduces the measured gap.
For example, in food the maximum roughness required is very often a Ra of 0.8μm. Indeed, the infractuosities of the raw sheet can be the seat of the development of bacteria, which can be dangerous for your process. To go further in polishing, an electrolytic polishing can be done by chemical process. To prepare this step, the automatic polishing must be carried out with a ra of 0.4 μm maximum, all the microns gained in preparation are important for this phase.